Amorphous metal core
Features & Benefits
Crafted with decarbonisation in mind

Most energy-efficient transformer in Europe

Lowest combined Load and No-Load Losses
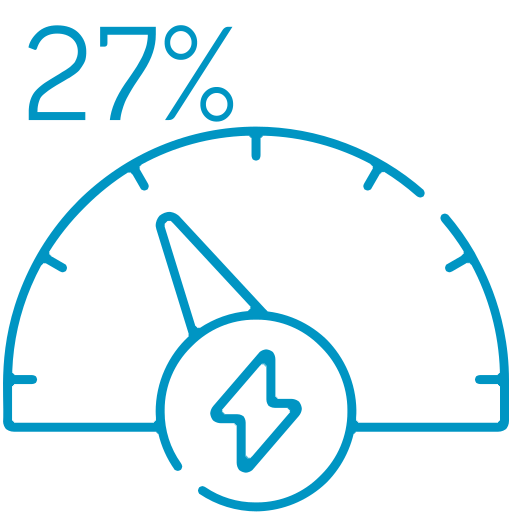
27% lower losses compared to Ecodesign Tier 2

16 years of proven track record and 0 core failures
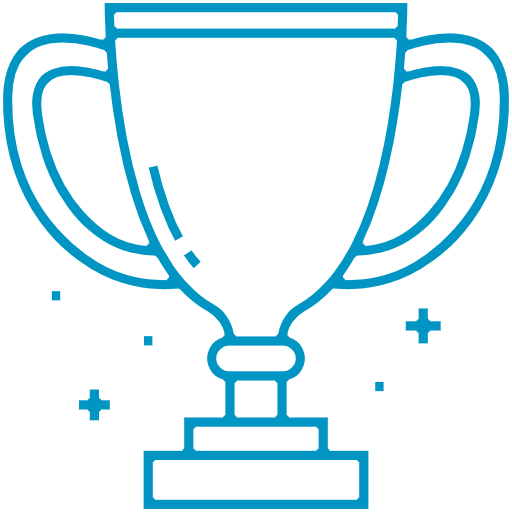
Award-winning transformer technology

Over 2000 amorphous installations across the UK

Short payback periods

Unparalleled carbon and energy savings

On-load tap changer option available with Wilson e4+
Fully customisable options available on request

Liquid-immersed (ONAN or KNAN)
Payback Calculator
Europe’s most efficient distribution transformer
Upgrading to Wilson e4 Ultimate Low Loss Amorphous® Transformer provides you with substantial carbon, energy and financial savings. Use our payback calculator to find our potential savings.
Your Transformer Savings
This is compared to your existing transformer, with a kVA rating, % load factor and £ per kWh initial tariff.
-
£
-
kWh
-
tonnes CO₂e
-
£
-
kWh
-
tonnes CO₂e
Get more details
Fill out the form below to receive a breakdown of the annual energy, carbon and financial savings
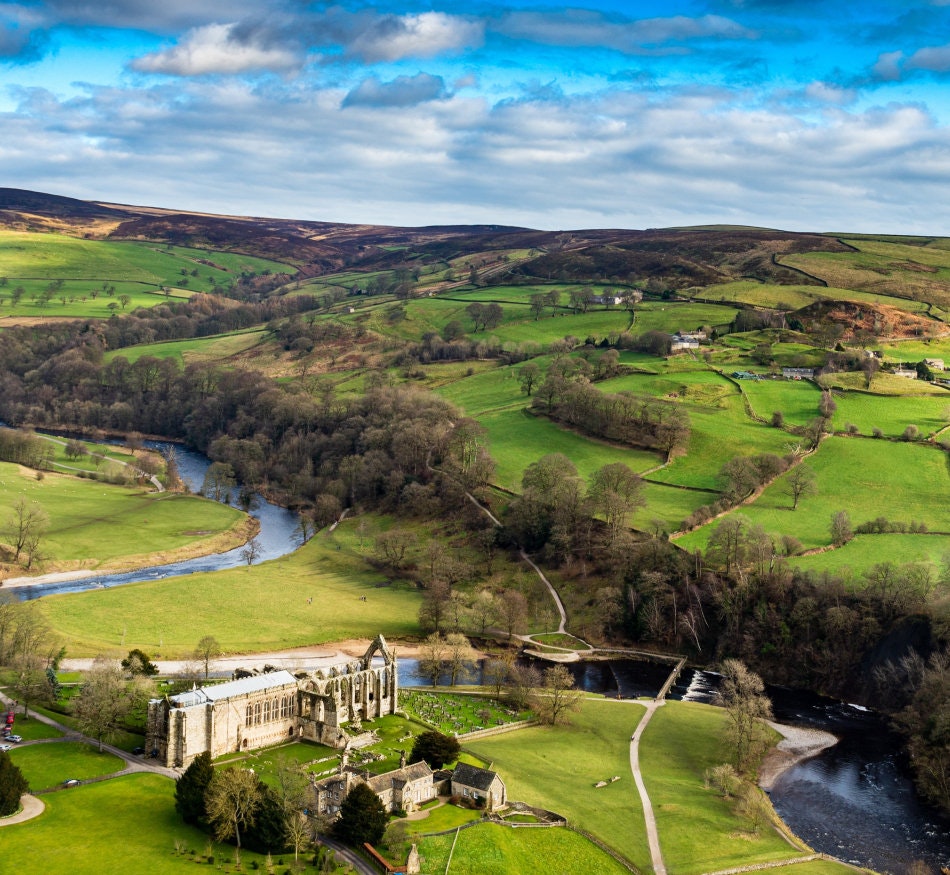
Your tonnes CO₂e visualised:
times
kettle's boiled
miles
driven in a car
flights
London to San Francisco
Product Information & GA Drawings
Select Transformer Rating for Product Info
View full product information including specifications, ancillaries, data sheets and GA Drawings. Please select the power rating of the suitable transformer.
Select Power Rating:
Ancillaries
Projects
Helping organisations reduce carbon emissions
Related Products

Wilson e4+ Ultimate Low Loss Amorphous® with OLTC
Up to 3MVA with Constant LV
On-Load Tap Changer with customisable HV tap change positions

Packaged Substations
MV Switchgear, LV Cabinets and Feeder Pillars
RMUs up to 36kV and ACBs & MCCBs up to 3200A
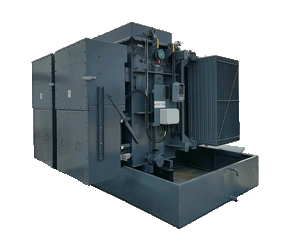
Bespoke Transformers
Fully customisable transformer design, manufactured to order
Special voltages, core materials, windings and others

We're here to help
If you need further information or additional product details, talk to one of our regional sales managers today.
